The RoHS directive is forcing manufacturers to use
lead-free solders to manufacture a wide variety of electrical
equipment. All lead-free solders are “different” to tin/lead
solder but as yet there are no clear guidelines or standards
for lead-free solder circuit design. Design engineers
searching for publications recommending designs for pads,
tracks and board layout specifically for lead-free will find
very little information.
This lack of guidance does not, however, mean that PCB
designers can ignore the change to lead-free solders.
Profound changes need to be considered when designing new
products.
Many manufacturers who have already re-designed their
products for lead-free processes have found that changes to
circuit design do not need to change, but this is not always
the case, especially with more complex PCBs. This short
article is intended to indicate where design changes might be
needed and how lead-free solders might influence circuit
design. 1 Components
- Material changes: The main change has been to
change tin/lead terminations to a lead-free substitute,
which is often tin. For many components this is the only
difference and will not affect the maximum reflow
temperature of the component.
- Maximum reflow temperature: The temperature above which
components distort or are permanently damaged depends mainly
on the choice of materials within the part. Plastics, for
example, are susceptible to high temperature and either
degrade or melt and both these can degrade or destroy the
function of the component. As lead-free solders require a
higher reflow temperature than tin/lead, a wide variety of
components may be unsuitable for use unless component
manufacturers have modified these parts to increase their
maximum reflow temperature. Most components are
converted to comply with RoHS simply by changing tin/lead
termination coatings to tin but changes to withstand the
higher temperatures required are more difficult and often
this is unchanged. This has a significant impact on circuit
design if the reflow temperature that has to be used for a
particular PCB is higher than the maximum reflow temperature
of a component, as this component cannot be used. If a
substitute with the same function is not available from
another manufacturer, then re-design will be necessary.
There are two possible options here;
- Redesign circuit so that heat sensitive components can
be attached using selective soldering or hand soldering
after all other components have been attached, These
soldering techniques do not heat components to as high a
temperature as SMT but require space around the
component.
- As a last resort, the heat sensitive component will
have to be changed to a different type, which often
requires significant circuit design changes. SMT
electrolytic capacitors are examples of particularly heat
sensitive components.
- Part numbers: Some component manufacturers show
this change by a different part number, a code prefix or
suffix but some have not made changes to part
numbers
- Component obsolescence: Many older types of component,
particularly ICs may not be available as lead-free versions.
In some cases, the demand for components is low and RoHS has
reduced this to a level where the manufacturer decides to
make it obsolete. In either circumstance, this will
necessitate circuit redesign to accommodate alternative
components. Re-plating leadframes with tin is possible but
expensive and so not usually an option. Software
rewrite may also be required for processor ICs. Early
component obsolescence is increasingly an issue for
electronics manufacturers. Life-time-buys are an option as a
last resort but are usually unacceptable in the longer term.
Some circuit designers of equipment intended to be on
the market for many years are planning for such
eventualities by designing circuits in such a way that when
a critical component becomes obsolete, it can easily be
replaced by a substitute.
Back
to top
2 Behaviour of lead-free
solders
Lead-free solders are different to tin/lead in several
ways, the main differences being:
- Higher melting point – typically 30 - 40°C higher -
Inferior wetting properties, mid-chip solder balls -
Higher surface tension – increased risk of tomb-stoning and
bridging
- Issues arising from higher temperature lead-free
processes. All thermal effects increase with
temperature:
- Multiple heat cycles, pad solderability and component
damage - Double sided PCBs may have two SMT reflows plus
one wave soldering followed by selective soldering and
hand soldering. Pads may be unsolderable after three
lead-free reflow cycles as surface oxidation is increased
at the higher lead-free temperature. Design should aim to
minimise heat cycles. Components attached in the early
heat cycles may be damage during later cycles if
over-heated.
- DT across pcb: This is an issue with surface mount
reflow.
- PCB warping
- Cracks in PTH
- Inferior wetting – smaller pads but as bridging is more
likely, pads need to be elongated and spacing between pads
increased.
- Poor wetting of vias and through holes – alleviated
- Tomb-stoning occurs with tin/lead solders for a variety
of reasons. The risk of this occurring with lead-free
solders is increased due to the higher surface tension of
these alloys and so the techniques used avoid this defect
with tin/lead solders are even more important with lead-free
solders.
Back
to top
2.1 Additional Suggestions:
- Increase spacing between pads to minimise risk from
bridging
- Align multi-pin components parallel to solder transport
direction
- As wetting is inferior, use smaller pads to ensure that
no pad areas remain without solder. This will be important
for equipment used in corrosive environments. “Rounding” of
corners of pads helps prevent thermal decomposition of flux
at higher lead-free temperatures
 |
Tin - lead SMR pads |
Smaller lead-free SMT
pads |
- Use "thief pads" to reduce risk of bridging
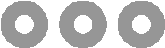 |
|
Plated through hole pads |
Elongated PTH pads to avoid
bridging |
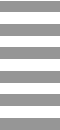 |
|
Tin/lead |
Lead-free |
Elongated IC pads and larger end pads to act as thief pads
to reduce risk of bridging
- Use modified pad shape to reduce risk from mid-chip
solder balls
Stencil aperture design recommended by Cookson Electronics to reduce risk of
mid-chip solder balls.
3 PCB Design issues
There are no new formal standards for design of PCBs that
use lead-free solders, but component manufacturers will
include (in their technical datasheets) the dimensions of pads
that they recommend for their components. These should
be used unless modifications as described above prove to be
necessary or these problems are suspected from previous
experience.
There are several other issues that should be considered
for PCB design.
- PCB warping – The higher reflow temperature required
for lead-free increases warping of laminate. At high
temperature, the laminate becomes soft in reflow ovens with
conveyers that support the sides of panels only, these are
likely to sag in the middle. This can cause some components
to have poor solder bonds and to produce warped boards. One
approach suggested by NPL is to use a support wire along the
length of the reflow oven. These prevent boards from sagging
in the centre;
- Vias and plated through holes are stressed during
reflow because the thermal coefficient of expansion of the
laminate in the direction perpendicular to the board is
greater than that of copper. This can cause cracks and open
circuits, particularly if the hole drilling or plating are
of poor quality. This risk increases with reflow temperature
and is more likely with lead-free but can be reduced by
using:
- Larger hole diameters
- Thinner laminate
- Avoid paste in hole connectors (use wave or hand
soldering)
- In most reflow ovens, the temperature at the sides is
lower than at the centre. Therefore avoid locating large
components at the edge and small heat sensitive components
at the centre.
Dr. Paul Goodman Senior Materials Consultant
Reliability & Failure Analysis Back
to top |